At its core, CNC milling involves the removal of product from a workpiece through a collection of collaborated activities. The process begins with the layout of a 3D model using computer-aided design (CAD) software program. This version functions as the plan for the milling device. Once the design is finished, the operator uses computer-aided production (CAM) software application to equate the CAD version into a collection of directions that the CNC machine can review, commonly in the type of G-code. This code determines the motions of the maker's cutting tools, such as pin turning and feed rates, making certain that every cut is replicable and precise.
One of the standout attributes of CNC milling is its convenience. Unlike conventional milling machines, which usually run along one or two axes, CNC milling makers can operate on numerous axes concurrently-- commonly 3, 4, or also 5.
Discover cnc milling guide the transformative globe of CNC milling, an innovation that integrates precision and automation to generate high-quality parts successfully from numerous products, and uncover its procedures, advantages, and key factors to consider for success in contemporary manufacturing.
The choice of tools is an additional crucial aspect of CNC milling. There is a variety of cutting tools available, including end mills, face mills, and sphere mills, each fit for various applications. End mills, for instance, are versatile devices that can be used for side and face cutting, while ball mills are suitable for developing rounded edges and complicated contours. The suitable tool option can greatly impact the quality of the ended up item and the effectiveness of the machining process. Additionally, proper tool upkeep and condition monitoring play a substantial role in maintaining optimum performance and prolonging device life.
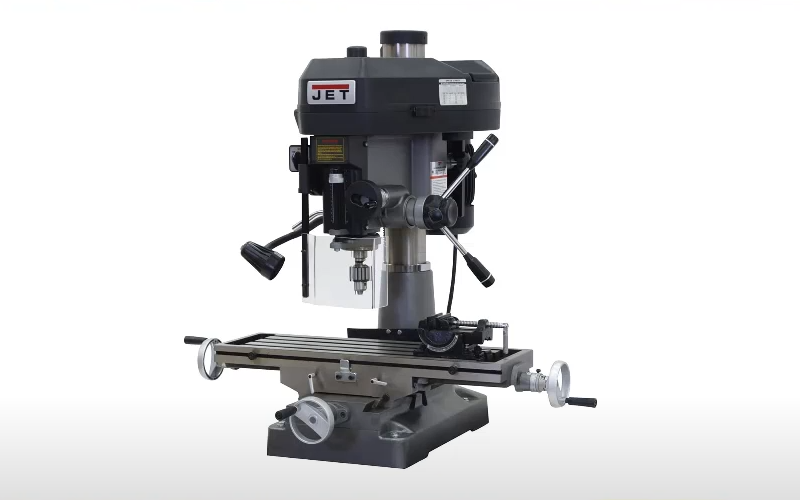
One important variable to think about in CNC milling is material compatibility. Depending on the type of product being machined, specifications such as cutting rate, feed price, and tool option might need to be adjusted as necessary. Soft materials like plastics can frequently be machined at greater rates compared to tougher products like steel, which require slower rates and even more durable tooling. Understanding the residential or commercial properties of the product, including its solidity, machinability, and thermal conductivity, enables operators to optimize the milling procedure and achieve premium outcomes while minimizing damage on devices.
Beyond the technological elements like layout, tooling, and materials, there are added considerations for maximizing CNC milling operations. Work preparation is important, as it encompasses whatever from device selection and configuration to scheduling and operations administration. Reliable work planning can bring about higher performance, minimized lead times, and improved total efficiency. Utilizing innovative functions such as toolpath optimization techniques can enhance the milling process even more, making it possible for quicker machining cycles and decreasing waste.
One of the considerable benefits of CNC milling is the ability to automate repeated jobs, which decreases human error and improves manufacturing consistency. While standard milling machines need an experienced driver to supervise the manufacturing process, CNC milling makers can run neglected, performing pre-programmed directions with accuracy. This degree of automation not only enhances efficiency however also liberates experienced workers from ordinary tasks, enabling them to concentrate on better tasks such as quality assurance and process renovation.
Regardless of its benefits, transitioning to CNC milling is not without obstacles. Initial monetary investment can be significant, with expenses related to getting CNC machines, software, and proficient employees training. Nonetheless, many companies discover that the lasting cost savings related to boosted performance, decreased product waste, and boosted item quality outweigh the first prices. The availability of leasing choices and affordable entry-level CNC milling devices has actually made it extra accessible for small and mid-sized businesses to embrace this modern technology.
Training and ability growth for workers operating CNC milling machines are likewise crucial for maximizing the roi. Operators require a solid understanding of both the CNC device itself and the software being used for programming and surveillance. Lots of producers locate success by providing internal training programs or partnering with outside training companies to furnish their teams with the essential abilities and knowledge.
In recent years, technological improvements continue to form the field of CNC milling. As sectors progressively transform to automation, incorporating attributes such as man-made intelligence (AI) and maker learning right into CNC machines can additionally improve the accuracy and efficiency of milling procedures.
Advancements in software application are continually tightening the void between layout and manufacturing. Modern CAD/CAM systems currently give a lot more intuitive user interfaces and enhanced simulation abilities, permitting drivers to visualize machining processes prior to they are executed. By discovering possible concerns in the design phase, firms can fix layout flaws or optimize cutting methods without incurring costly modifications to physical products.
In the context of CNC milling, sustainability is also acquiring value as suppliers seek methods to decrease their environmental impact. Carrying out methods such as optimizing reducing criteria, using a lot more reliable tooling, and recycling materials can add to a more sustainable milling procedure. In addition, innovations such as additive production are being explored in conjunction with CNC milling, offering chances for hybrid manufacturing approaches that further enhance sustainability by decreasing waste.
Check out benchtop milling machine the transformative globe of CNC milling, a modern technology that combines accuracy and automation to generate high-grade parts effectively from various products, and uncover its procedures, advantages, and crucial considerations for success in modern manufacturing.
Finally, CNC milling stands for an essential asset in modern-day production, supplying business with the ability to generate complex and top quality components effectively. Its combination of automation, precision, and convenience has actually made it a staple in industries varying from aerospace to automobile, medical to customer items. Comprehending CNC milling begins with a solid foundation in its procedures, consisting of the interaction between layout, tooling, products, and software application. As technology continues to advance, the possibility for proficient operators to take advantage of these developments will just broaden, permitting for higher efficiencies and technologies in CNC milling applications. By remaining notified on best practices and arising technologies, producers can position themselves at the leading edge of this dynamic market and fully make use of the capabilities that CNC milling uses. Inevitably, successful combination of CNC milling machinery, proficient workforce training, and wise automation leads the way for the future of manufacturing, where top quality, sustainability, and effectiveness end up being the characteristics of functional excellence.